Rotor structure and strength testing services
As rotating machinery develops and is applied at high and ultra-high speeds, the strength and safety of high-speed rotors under centrifugal force are increasingly valued. Rotation tests exceeding operating speed, destructive rotation tests, and cyclic fatigue tests have become important means of assessing their strength and safety.
Our company's independently designedHLSTS series high-speed vertical rotor testercan drive the rotor to rotate at high speed and absorb the vibration energy when the rotor is overspeed and the huge impact energy when it is destroyed by flying apart. Currently, we mainly undertake rotor testing services in the following areas:
1) Inspection overspeed test of finished rotors (including high-temperature overspeed test)
Tests where the rotor is accelerated to above the maximum operating speed and maintained for a period of time are collectively known as overspeed tests. Typically, the overspeed test is 110%~120% of the maximum operating speed. Depending on the test task and purpose, overspeed tests mainly include: quality control and operating speed verification tests; elimination of residual internal stress; and during rotor operation, the tester can heat the test piece environment temperature to the range of room temperature~800℃.
2) Destructive testing of rotors (including high-temperature rupture test)
To assess the reliability and ultimate strength of the rotor under high-speed rotation. In the destructive test, the rotor is rotated at high speed, simulating the actual working environment of the rotating components, and the speed is continuously increased until destruction. The destruction test can provide data on many aspects, such as checking design defects, identifying weak links in the test piece, providing a basis for material selection, reducing manufacturing costs, strength failure analysis, limit assessment and safety margin confirmation. During rotor operation, the tester can heat the test piece environment temperature to the range of room temperature~800℃.
3) Rotor pre-stress treatment, improving the plastic limit of the material
High-speed rotating components of mechanical products will produce deformation or size changes during operation, thereby changing the original state and size matching, reducing the operation performance and reliability of the mechanical products. To solve this problem, pre-stress treatment is applied to the rotating parts to strengthen the rotor material, ensure stress uniformity, and passivate cracks, thereby reducing the rotor defect rate and increasing rotor life.
4) Low cycle fatigue test
To assess the actual service life of the rotor system. The stress level on the components is high, and the number of destructive cycles is generally less than 104~105fatigue between, such as the fatigue of aero-engine impellers, gas turbine impellers, etc. Practice shows that the greater the fatigue life dispersion, the more necessary it is to perform a quantitative analysis of the rotor's life, which requires testing the rotor's fatigue life.
Mainly used in aviation, automobiles, turbomachinery, medical, high-speed motors and other fields.
Application equipment fields mainly include
• High-speed motor | • High-speed centrifugal pump | • Turbo expander in air separation equipment | • Turbocharger in marine diesel engines |
• High-speed centrifugal turbo compressor | • Aero-engine | • High-speed centrifugal fan | • High-speed rotor energy storage battery |
• Nuclear industry gas high-speed centrifugal separator | • Medical high-speed centrifuge | • Automotive engines and other rotating machinery |
The compressor wheels, expander wheels, turbines, impellers, rotors, and centrifugal rotors of the above equipment mostly have high operating speeds (usually 20000rpm~50000rpm). Under such high speeds, the stability and safety of the rotor system must be ensured. Overspeed, rupture and fatigue tests have become an indispensable part of product research, development, production and fault diagnosis.
Figure 1 Physical diagram of a high-speed motor rotor assembly state and rupture state (rupture speed 28500rpm)
Figure 2 Physical picture of the heating system and rotor installed
Case study and test report of overspeed rupture test of a new energy motor rotor
Figure 3 Test case report of a high-speed motor rotor (rupture speed 36860rpm)
Our company can provide users with rotor test tooling design and calculation and analysis, tooling processing, assembly, dynamic balancing, rotor test testing, and provide test reports. We provide users with fast response and service for product development and testing, and the recovery time after the test bench explosion is within one day (under the condition that the tooling is fully prepared).
Parameter introduction of HLSTS100 series high-speed vertical rotor tester
• Drive power: 100kW
• Speed range: 0~60000rpm
• Speed control accuracy: ±0.05%FS
• Maximum diameter of test piece: 1000mm
• Maximum height of test piece: 700mm
• Maximum weight of test piece: 200kg
• Vacuum degree in test chamber: Absolute pressure less than 100Pa
• Maximum test temperature: 750℃
• Test temperature control accuracy: ±2℃
National Service Hotline:86-731-28827966
Address: Tiantai Jingu Industrial Park, 152 Huanghe South Road, Tianyuan District, Zhuzhou City, Hunan Province
E-mail:18670821903@163.com
Social Media
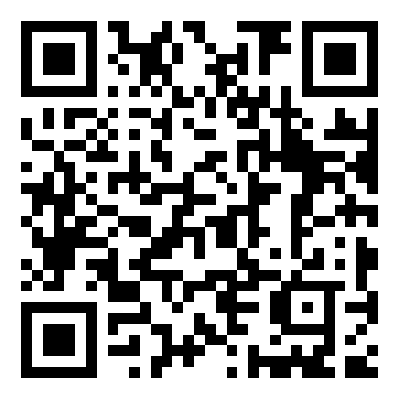
Mobile website
Copyright @ Hunan Hangli Transmission Machinery Co., Ltd.
The website supports IPv4 and IPv6 bidirectional access